スカイアクティブエンジンの導入に合わせてマツダは、シリンダーヘッドの製造に砂型鋳造を導入した。 主なねらいは設計値どおりの燃焼室や冷却水路を正確に量産することだった。 金型と違って砂型には保温効果があり、溶けたアルミが隅々まで行きわたるというメリットがある。
TEXT&PHOTO:牧野茂雄 (Shigeo MAKINO)
シリンダーブロックとシリンダーヘッドの製造は、金型鋳造(ダイキャスト)が主流である。金型内に複雑な形状の中子を組み込み、そこに高圧で溶けたアルミを圧送する高圧鋳造(ハイプレッシャー・ダイキャスティング=HPD)の技術が進歩し、正確な鋳物を作ることができるようになった。また、成形対象によっては低圧鋳造(ロープレッシャー・ダイキャスティング=LPD)という手法もあり、これも一般的には利用されている。
その時代にマツダは、最新技術を投入したスカイアクティブエンジン群の製造に砂型鋳造という方法を選択した。二液性硬化樹脂を混ぜた特殊な砂を使い、シリンダーヘッドの外観形状となる砂箱と、ディーゼルエンジンは13個、ガソリンエンジンは12個の中子を作り、型を組み立てる。燃焼室の天井となる面、砂型を積み上げていくときのベースプレートは金属製の鋳型を使い、精度の高いサンドパッケージを作る。吸気/排気ポートや冷却水路を設計値どおり正確に成型するため、精密な中子が人の手によって組み込まれる。そのサンドパッケージにアルミ合金の溶湯を注ぐ。
サンドパッケージの上面から自由落下で溶湯を注ぐ重力鋳造ではなく、側面からほんの少しだけ圧力をかけて溶湯を流す超低圧鋳造である。製造現場を見れば、アルミ溶湯を押し込むストロークはわずか50mm程度であり、ほぼ重力鋳造である。溶湯を流し込みながらサンドパッケージ全体を一度だけ上下逆になるよう回転させ、砂型内部の隅々にまで溶湯を行きわたらせる。
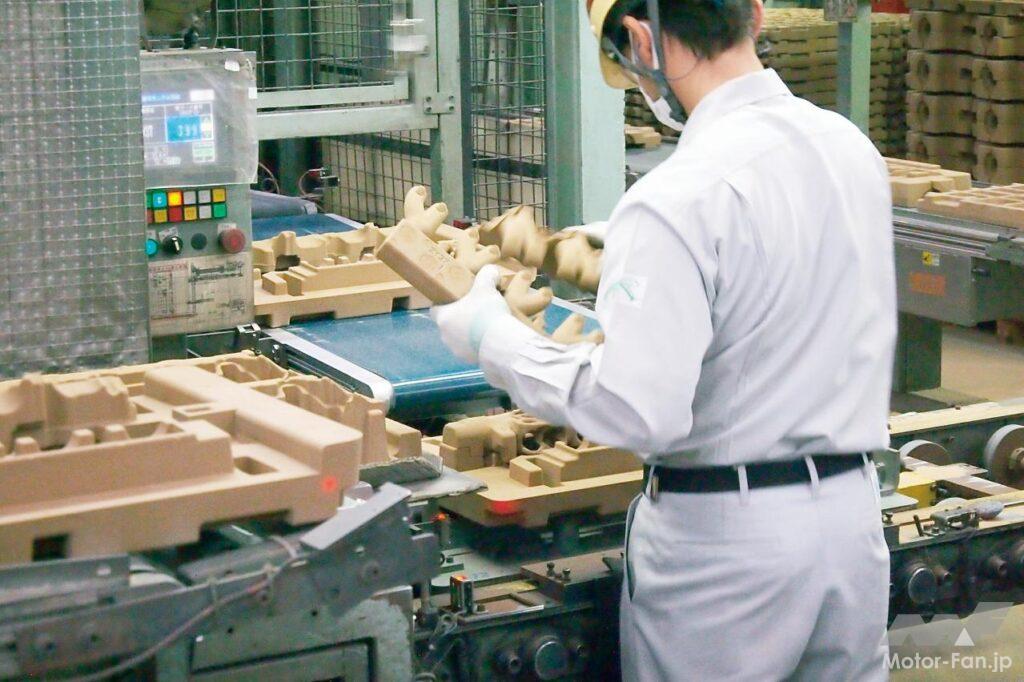
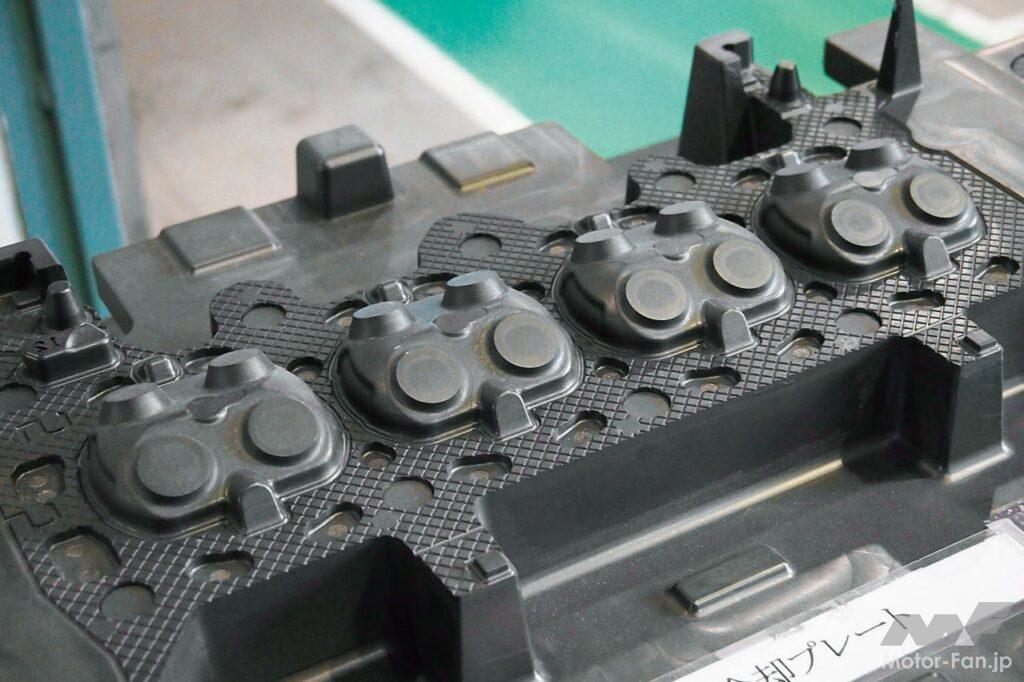
なぜ砂型なのか。理由は大きく分けて3つある。まず、要求される機械的性能を忠実に作り込むことだ。燃焼室面となる部分を冷却性に優れた金型ベースプレートとし、この部分は金属の表面急冷効果を利用してアルミの組織を緻密にする。それ以外の部分は砂型ならではの表面仕上がりをねらう。冷却水路やポートの部分は、金型鋳造するだけでは不可能なくらいの薄肉化、機械加工でなければ実現できないレベルの薄肉化を実現する。
ふたつめは、つねに同一条件で鋳造することだ。砂型も金属金型のベースプレートも管理された常温で使用されるため、アルミ組織内の引け巣やリーク不良のリスクが極めて少ない。想像しにくいかもしれないが、保温効果のある砂型のなかに溶湯を注ぐと、凝固してしまう前に隅々まで溶けた金属が回る。金型だと溶湯の熱を素早く奪うため引け巣ができやすい。日本の製造技術はここを克服しているが、それでも砂型を使うメリットはまだある。
3つめは、上記の2点を実現したうえでの成形サイクルタイム短縮化である。LPDの場合はシリンダーヘッドの成型に7分程度の時間を要するが、マツダは溶湯充填と凝固冷却の工程を分離したコスワース鋳造法であり、砂型への溶湯充填だけで見れば約1分である。
コスワースエンジン鋳造で鍛えられた腕
マツダはフォードと資本提携していた関係から、コスワースのシリンダーブロックを成形した経験がある。15年ほど前のことだが、このときに常温砂型を使用する経験を積んだ。砂型鋳造では「シリンダーヘッドをうまく作れるようになれば一人前」と言われるが、コスワースエンジンの製造でマツダはこれを学んだ。その経験がスカイアクティブエンジンの製造で役に立ったのである。
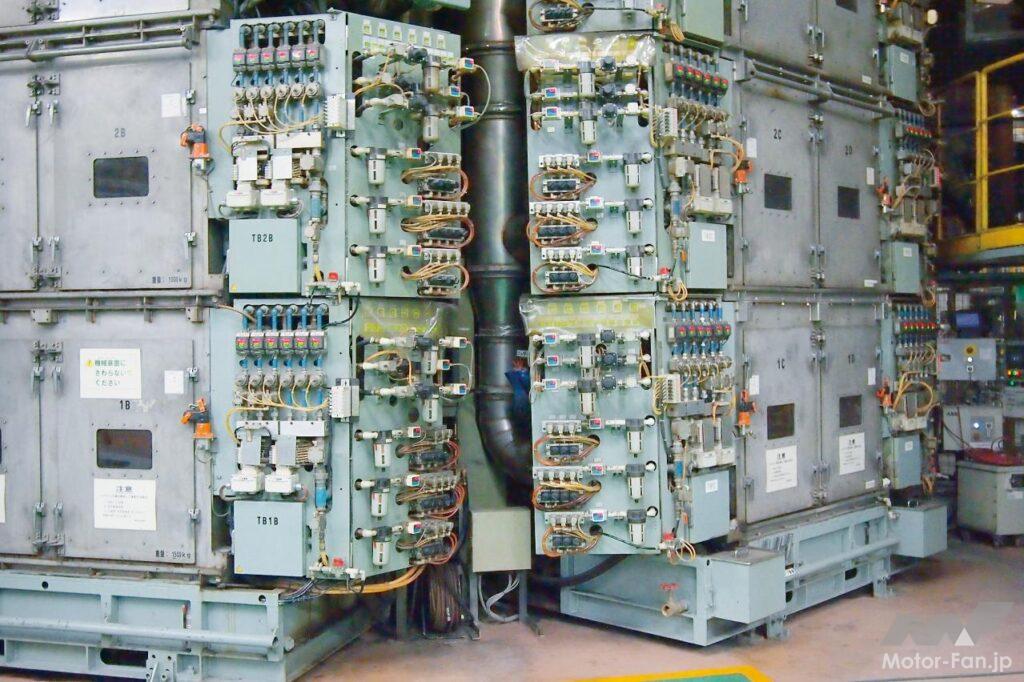
もっとも難しいのは、砂型に溶湯を注いだあとの冷却である。冷水プールにどぶ浸けする方法では砂型内の温度が均一に下がらない。マツダの現場では「実際に計測してみると、熱が逃げるのは表面の一部であり、早く冷める部位とゆっくり冷める部位とで温度変化の時間がかなり違う」と訊いた。そのためマツダは、サンドパッケージを冷却室に入れて水のシャワーを浴びせ、温度変化を厳格に管理しながら冷ます方法を採用した。
まず、サンドパッケージの上からシャワーを浴びせ、遅れて(2分程度だった)下面の金属ベースに下からシャワーを浴びせる。この時間差が肝らしい。そこから、均一に冷えるよう制御した順番でつぎつぎとシャワーを浴びせて5~6分間の強制冷却を行なう。そのあと冷却室からサンドパッケージを出し、自然放熱させる。約2時間の放置で20~30°C下がるそうだ。「これでは成形時間が短くても後工程が長過ぎるのでは」と思ったが、「LPDでも凝固・冷却の時間は必要であり、トータルでは時間短縮になる」と聴いて納得した。
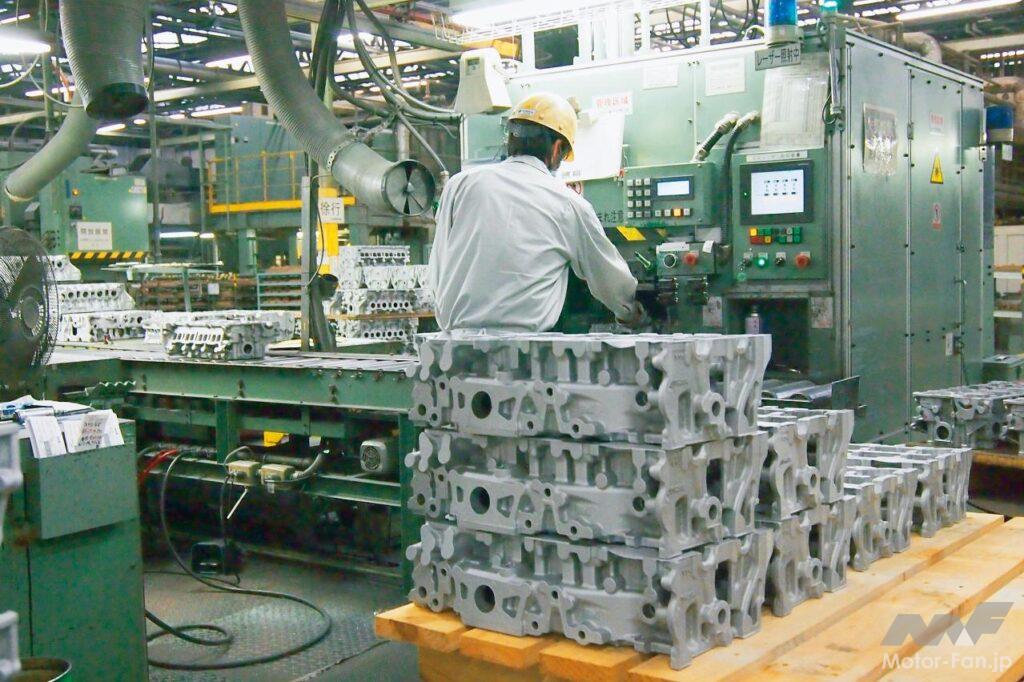
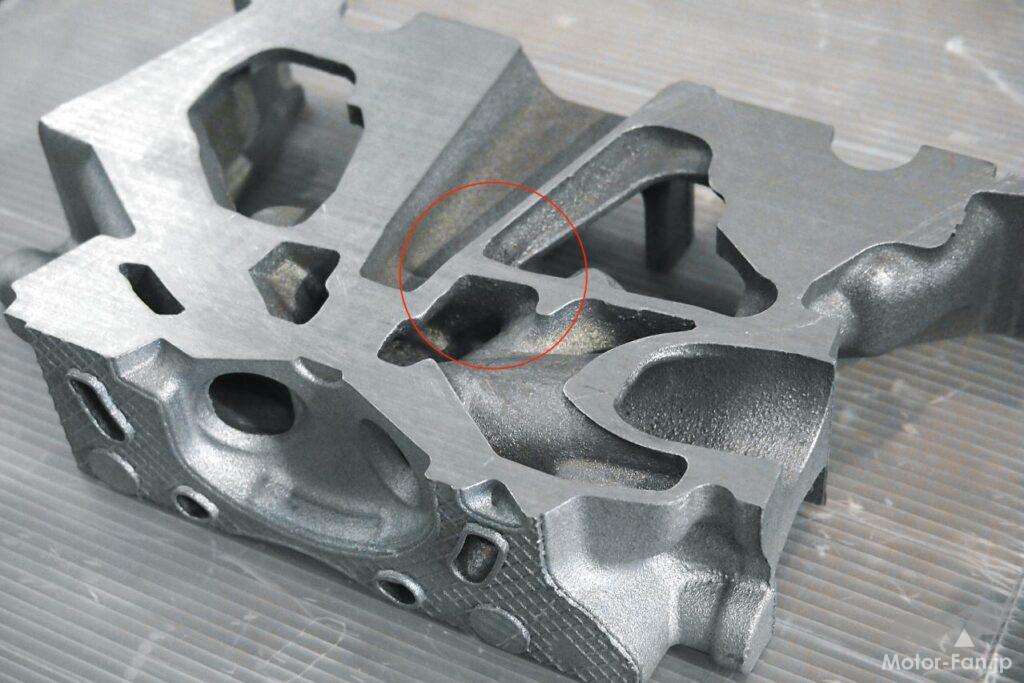
冷ましたあと、砂型を壊して鋳物を取り出す。サンドパッケージを14G程度で揺すると、砂と砂、砂とアルミがぶつかってどんどん砂が落ちていく。表面にこびりついた砂は超音波で取り除く。鋳造済みの砂は焙焼して使いまわし、一回の成形で失われるのは全体のうち2%程度だという。二液性硬化樹脂を混ぜた砂だが、その樹脂成分は溶湯が注がれると熱を奪って硬化するため、短い成形時間内に砂型の強度がどんどん高くなるそうだ。完成したシリンダーヘッドは、必要な機械加工を施されたのちにエンジン組み立てラインへ運ばれる。
かつてコスワースエンジンを作っていたときは、砂型を焼き固めるシェルモールディングを採用していた。丈夫な砂型ができるが、熱収縮を見込んで砂型を作る必要があった。スカイアクティブエンジン用の砂型は熱を加えないからシェルモールディングよりも型はもろいが、寸法精度が高く、しかも設計値と一対一の寸法で型を作ることができる。
そして、溶湯を注ぐときにサンドパッケージ全体を上下逆さにする「回転」を入れたことで、アルミ組織の緻密さは20μ、不良率は0.5%以下を達成した。優秀なLPDでも組織密度は約50μ、不良率2%と言われるから、マツダ方式の砂型鋳造の優秀さがわかる。もっとも、こうした製造工程の設計はシミュレーションだけでできるはずがなく、さまざまな試行錯誤を経てたどり着いたものだ。コスワース鋳造法の経験があったからこそ、「こうすれば良いのでは?」というアイデアが浮かび、噴出する問題点にも対応できた。「継続は力なり」のシリンダーヘッド造りである。
ひとつの砂型からエンジンを1基だけ作る。寸法精度にもアルミ組織にも個体差はほとんどないのだが、1対1の潔さには何となく魅力を感じる。すべてがワンオフ。しかし均質な量産品。これが最大の特徴である。
からの記事と詳細 ( マツダ・スカイアクティブエンジンの精密砂型鋳造:シリンダーヘッドをわずか1分で製造[内燃機関超基礎講座] - MotorFan[モーターファン] )
https://ift.tt/iztFrZv
No comments:
Post a Comment